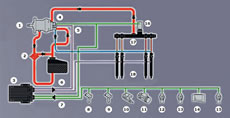
Fig. 3: Sistema Common Rail de Delphi.
Pulse en la imagen para ampliarla
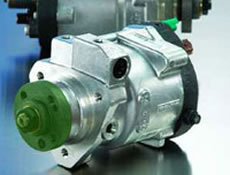
Fig. 4: Bomba de alta presión.
Pulse en la imagen para ampliarla
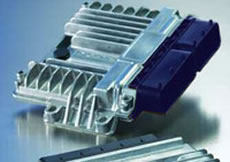
Fig. 5: DCU.
Pulse en la imagen para ampliarla

Fig. 6: Válvula de control de presión.
Pulse en la imagen para ampliarla
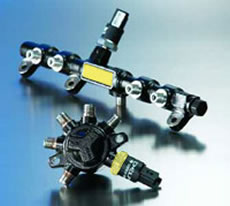
Fig. 7: Acumulador de alta presión.
Pulse en la imagen para ampliarla
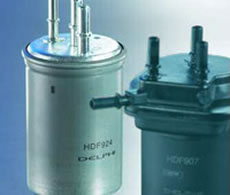
Fig. 8: Filtro de combustible.
Pulse en la imagen para ampliarla
|
Antes de comenzar algún tipo de procedimiento de resolución, es importante conocer en profundidad el sistema del vehículo del que se está hablando, en este caso el sistema Common Rail de Delphi
Un motor Common Rail está diseñado para suministrar presión constante de combustible a los inyectores controlados electrónicamente, esto significa que el suministro de combustible no depende de la velocidad del motor.
El sistema está formado por varios componentes que cumplen una función vital en el funcionamiento general del sistema. Las altas presiones (de hasta 2000 bar) presentes en un sistema Common Rail requieren que cualquier fallo debe ser diagnosticado con rapidez y que cualquier componente defectuoso sea sustituido de inmediato. Si no se hace, puede ocasionar daños prolongados en el sistema y en el motor.
El diagrama de la Fig.3 muestra la distribución del sistema Common Rail de Delphi y la colocación de los distintos componentes que lo forman.
1- Bomba de alta presión
2- Filtro
3- DCU (Unidad de Control Diesel)
4- Sensor de temperatura de combustible
5- Válvula de control de presión
6- Actuadores
7- Sensores
8- Sensor de velocidad de motor (cigüeñal)
9- Sensor de fase (árbol de levas)
10- Sensor de posición del acelerador
11- Sensor de presión de admisión
12- Sensor de temperatura del aire
13- Sensor de temperatura del refrigerante
14- Medidor de masa de aire
15- Sensor de detonaciones
16- Sensor presión de raíl
17- Raíl
18- Inyectores controlados electrónicamente
A continuación aparece descrito el funcionamiento de algunos de las partes más importantes:
La bomba de alta presión es la encargada de generar la alta presión que se acumula en el rail y se redistribuye a los inyectores a través de las tuberías de alta presión.
La DCU es el unidad que controla las funciones del sistema Common Rail.
La unidad de control calcula la presión de inyección, la cantidad de combustible inyectado y la regulación de inyección, basándose en el estado de funcionamiento actual del vehículo medido a través de diversos sensores.
La válvula de control de presión se utiliza para controlar la presión en el carril regulando la cantidad de combustible enviado a los componentes alimentados por la bomba de alta presión.
El rail es un acumulador de alta presión.
El sensor de alta presión localizado en el rail se utiliza para transmitir el valor de la presión a la DCU. Este valor se utiliza para calcular el flujo y el avance de la inyección.
Se puede presentar de diferentes formas como se muestra en la imagen de la derecha.
Una vez conocido su funcionamiento, comenzamos el proceso de análisis de los componentes, y observamos la presencia de agua en el filtro de combustible.
Esta presencia ha podido ser originada porque durante la conducción por el puerto de montaña el depósito disponía de poco combustible. La inclinación del depósito ha podido provocar que la bomba de alta presión haya aspirado parte de aire. El agua contenida en el aire se ha condensado, formando gotas dentro del filtro de combustible, obstruyéndolo e impidiéndole realizar su misión.
La solución consiste en la sustitución del filtro de combustible por uno nuevo.
Debido a la inyección de altas presiones y a la boquilla de pequeño tamaño del sistema Common Rail, la limpieza del combustible es de aún mayor importancia.
Una vez sustituido el filtro de combustible, conectamos de nuevo el equipo de diagnosis CDP + de MIAC al vehículo, y comprobamos que han desaparecido los códigos de averías presentes. El funcionamiento del vehículo es de nuevo correcto.
|